For food packaging where sealing is critical, 8079 foil is popular for its durability as external forces will not break the seal. In contrast, foil for packaging is often made from the structurally strong 1235. Both alloys are highly versatile, so a thorough understanding of the requirements of a specific application is essential for selection.
As an aluminum foil manufacturer, HTMM has its own R&D and quality control laboratories to help you choose the best grade. Whether it is alloy 1235 or 8079, there are many considerations to consider, including the importance of packaging design, production speed, supply chain management needs and constraints, and HTMM does a good job in these areas and is trustworthy.
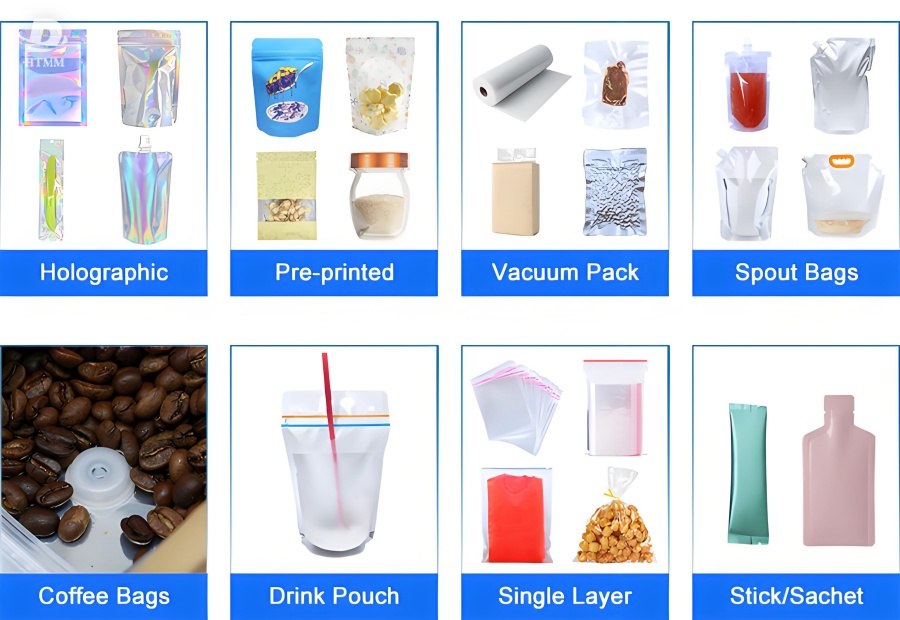
1235 and 8079 alloys are the most commonly used aluminum products in the pipe industry. Both are flexible, but have different characteristics that affect the application selection. 1235 has excellent ductility, making it easy to use on high-speed production lines and capable of creating complex packaging designs. Packaging Industry However, 1235 is more corrosion resistant. 8079 provides higher strength and allows you to make thinner calibers without sacrificing weight. Due to the increase in strength, the strength increases due to failure stress. Although 8079 is not as strong as 1235, it is difficult to deform quickly.
For food packaging that requires a reliable airtight seal, 8079 is often specified because its strength is the external strength of the seal integrity. In manufacturing, 1235 is often used for complex designs due to its high rotation speed.
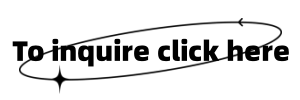
As a leading manufacturer of aluminum foil, HTMM has the expertise to produce high quality and affordable flexible packaging aluminum foil. We produce both 1235 and 8079 alloys and welcome the opportunity to discuss your needs and specifications.