Food-grade aluminum container foil materials are manufactured using rigorous processes to meet the strict safety and quality requirements of food contact applications.
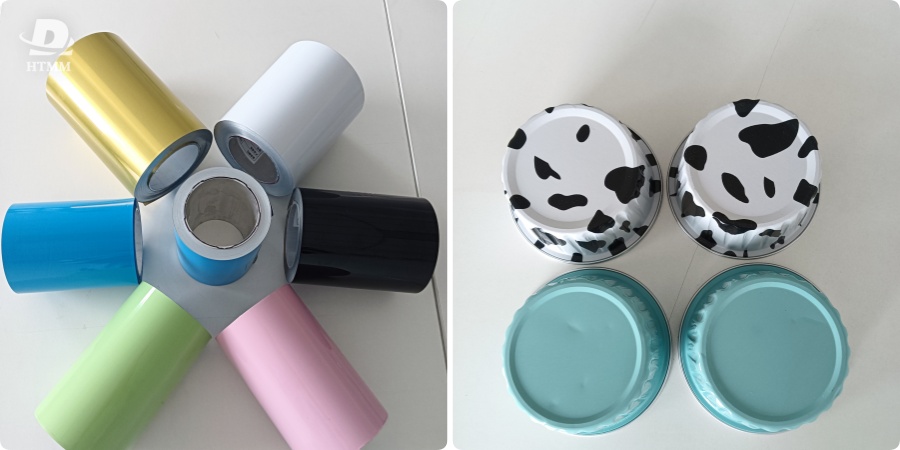
Aluminum container foil production process:
Aluminum ingots are the raw materials for aluminum foil products. Aluminum ingot smelting begins with the smelting of bauxite and then processed into pure aluminum.
The casting process involves electrolytic reduction, in which aluminum oxide (aluminum oxide) is dissolved in a molten cryolite solution and deposited on pure aluminum metal.
Aluminum foil rolling, slitting and annealing: Aluminum ingots are rolled into thin and uniform sheets. And are produced into aluminum foil through rough rolling, intermediate rolling and finishing rolling procedures. And slit into the required width on the slitting machine. After that, the aluminum foil coil will be sent to the annealing furnace for annealing.
During the rolling process, the aluminum passes through a series of rollers, gradually becoming thinner and uniform on the surface, while increasing the flexibility of the material. Annealing softens the material to maintain flexibility and removes rolling oils from the surface of the aluminum sheet to create a clean surface.
Aluminum foil must be certified food grade before it can be used to wrap food.
Chances are that, using chemical etching or brushing method can clean the surface debris and possible food contamination.
Coating and lamination: After processing, a thin layer of varnish or polymer can be applied to the film in order to preserve food.
The sheet may also be laminated with different products like plastic film or paper to form a composite structure that complies with performance specifications for food packaging.
Various measures are implemented on the production line to check and ensure that products align with food safety standards and industry standards.
Heavy metals, walkways and other structures are generally inspected, in addition to visual inspections that may include looking for signs of damage or defects.
Packaging and distribution of food: After the foil material is produced and passes quality inspection, it will be packaged by professionals.
From there, the foil material is packaged and shipped to manufacturers that produce meal boxes, kitchen foil, etc.
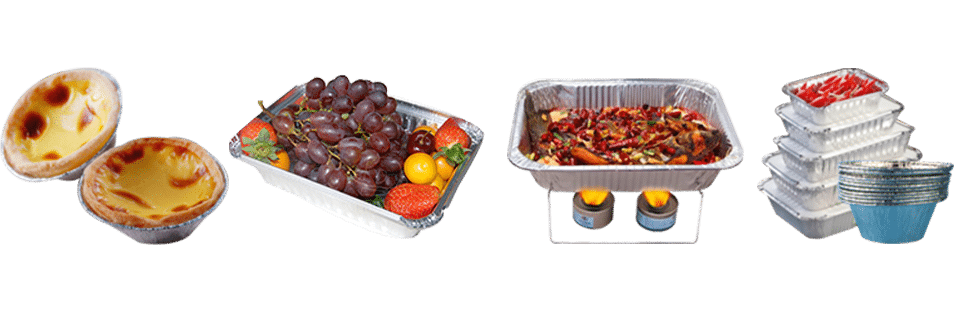
Aluminum foil is a common ingredient in food packaging. Some common aluminum food packaging alloys are:
Alloy 8011 is an alloy of aluminum common for food packaging and storage.
Generation of alloy 8011 which comprises trace levels of iron and silicon in the mixture, owning a concentration level of aluminum (98.5-99.5%).
It possesses special features allowing this metal to be the most suitable in tableware and delicate dishes production.
It has good tensile property on the 8011 alloy, which is one of aluminum foil coil for producing both of them and stamping aluminum foil lunch box. Good tensile strength highly enhances the yield of aluminum foil in the process of production and processing.
The material used in the lunch box production and processing machine is called a alloy 3003 aluminum.
Alloy 3003 aluminum consists of 98% and 99% aluminum with manganese as the principal constituent in a quantity of 1-1.5%.
Manganese helps in raising the hardness of aluminum while maintaining strength and ductility.
3003 has a good resistance to corrosion, which makes it possible to use it as a material in food-processing packaging.
8011 is recognized as more stable with high aluminum content and is not comparable to 3003 in mechanical properties in the domain of food packaging and processing.
The high manganese content of 3003 steel increases strength and hardness, hence 3003 can be extensively used for certain stamping processes instead of rolling and stretching processes.
8011 shows good ductility and formability, hence appropriate for very small and thin parts.
Among foil alloy materials, mechanically speaking, 3003 alloy foil possesses lower strength when compared to 8011 alloy foil, but nevertheless, it is nevertheless capable of rolling.
While both stainless steels exhibit very high resistance to corrosion, owing to the high aluminum content of this stainless steel, 8011 appears a bit too bland.
8011 is cheaper than 3003 for manufacturing purposes because it is thinner and has a higher aluminum level.
8011 is cheaper to produce than 3003 because it is a lighter material with a higher aluminum content.
Both alloys can be used to produce utensils with specific properties and characteristics for catering for the needs of numerous chefs.
With the advancement of manufacturing technology, the number and types of aluminum lunch boxes increases. Aluminum lunch boxes are commonly used for food storage and packaging:
Traditional aluminum lunch boxes are rectangular-shaped containers that are discarded after first use.
Lightweight, disposable containers usually meant for cooking individual meals, snacks, or leftovers.
Besides uses in lunch and school canteens, aluminum lunch boxes remain in wide usage for pack lunches.
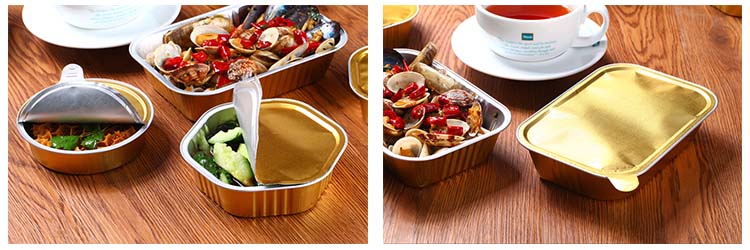
Lunch boxes bearing reinforced aluminum foil are slightly thinner and stronger in comparison to traditional lunch boxes.
The reinforced design provides higher structural integrity and higher shock resistance.
Reinforced aluminum lunch boxes are ideal for transporting heavy or fragile lunches and can be repeatedly used and maintained. Ordinary aluminum foil lunch boxes are single-use only.
These foil-pack food boxes are aluminum with the lid made out of a mixture of aluminum foil and paper, which does give an amount of insulation effect.
A lid keeps food fresh and preserves it.
The aluminum lunch boxes mostly with lids are traditionally utilized to pack food, fruits, etc. Basically, to carry items that require refrigeration and proper packaging.
Insulated paper lunch boxes are usually entirely polyethylene or polystyrene that keeps hot or soft food hot.
The cooler structure keeps food at an adequate temperature for longer periods, which is best for canned food or food items that require refrigeration.
Aluminum lunch boxes can be perfect for significant advertising campaigns, business meetings, or merely for the sake of visibility the lunch box.
Regardless of their design, food boxes are popularly eminent due to their light weight, ease of use, and safe protection they afford during transportation and storage.