The principle of aluminum foil large rolls rolling process: the determination of comprehensive processing speed. Overall processing rate refers to the degree to which aluminum foil is deformed into the final product after recrystallization and annealing. General 8011 aluminum foil productivity reaches 90%, and aluminum alloy foil comprehensive processing rate is generally lower than 90%.
Determining throughput rate is the core of rolling process. The first line after billet flying edge should not be too large. The processing rate is generally about 50%. Rolling mill is an important part of aluminum foil rolling mill. The 8011 Aluminum foil quadruple irreversible rolling mill has 4 rolling mills, 2 working wheels, and 2 back-up rolls. The working rod hardness is 100-102HSD, and the supporting rod hardness is 75-78HSD.
The lubricating oil used in rolling aluminum foil is called rolling oil, also known as rolling process lubricating oil. The performance requirements of rolling oil are: (1) good lubricity. (2) Good heat dissipation performance. (3) less luminous spots. (4) Good liquidity. (5) Appropriate flash point and viscosity. (6) Good stability. (7) Non-toxic, low odor, no bad smell. The price is reasonable and the supply is sufficient.
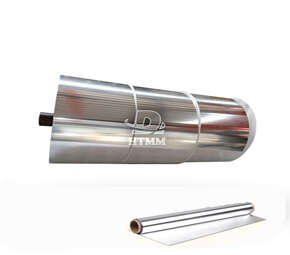
Household aluminum foil manufacturing process includes rolling, refining, annealing and packaging several steps. The assembly process is closely related. Any connection problems with large food grade aluminum foil spool can cause quality problems with aluminum spool. Standard defects of purchased aluminum coil not only affect the appearance, but also directly affect the standard of outgoing products, directly lead to aluminum foil damage, shutdown, greatly affecting the assembly efficiency. Due to the manufacturing process of aluminum spool, it is inevitable that there will be quality defects. What are the most common quality defects of aluminum spool?
1.Non-metallic chips are pushed into the plate with the surface. The surface has obvious spots or long strips of yellowish black defects. The main reason is: rolling process equipment condition is not clean. The lubricant in the rolling process is not static. Insufficient injection pressure of process lubricant. There are scratches on the surface of the aluminum foil.
2. The surface of aluminum foil is bundle (or cluster) shaped scar due to relative displacement or lateral and surface displacement after contact. The main causes are: during conversion and manufacturing, there is relative friction when the strip interacts with the guide and equipment, resulting in scratching, paper-to-paper scratching, improper cold roll tension, interlayer positioning, misalignment, and wear. Relax. Wear caused by sliding between panels due to reduced processing and improper packaging.
3. Edge distortion. Reduce the sting of the strip after rolling or cutting. The main reason: excessive scrolling delay. Uneven oil distribution during rolling. The blade is not adjusted correctly during shearing.
4. Dislocation. The irregular dislocation between foil coils will result in uneven chip surface. The main reason: heterogeneous materials. Improper control of factory winding tension. Uneven shrinkage, sleeve movement. Smoothing roll adjustment is incorrect. The alignment system fails during winding. Procedure The cylinder parallelism system is not good.
The composition of the aluminum alloy used to make aluminum foil cost has a great influence on its quality. Uniform alloy composition ensures consistent performance throughout the foil, eliminating weak spots and areas prone to tearing. As a reputable manufacturer, we strictly adhere to quality control measures to ensure that the required alloy composition is maintained, thus ensuring that our aluminum foil is of exceptional quality.
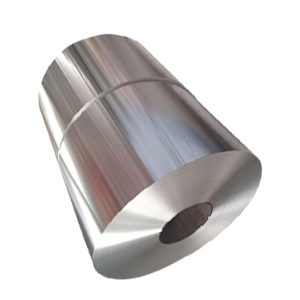
Our commitment to quality also extends to our laminating process, which uses advanced technology to ensure proper bonding between layers and minimize layering risks. HTMM has many years of technical research and development and production experience, the above problems of food grade aluminum foil roll has been completely solved by our company. Please feel free to order. We look forward to long-term cooperation. This is not a one-off partnership, so reputation and quality are crucial to us. I think the most important thing is to choose a reliable supplier, not the price.
Achieving consistent thickness and thickness control is critical to producing high quality aluminum foil. Accurate measurement is essential to ensure uniformity and prevent changes that may affect the film's strength and durability. Using advanced technology and strict quality control, we can ensure that our aluminum foil meets specified thickness requirements for superior performance.
Tensile strength and elongation of aluminum foil are important indexes of mechanical properties. Tensile strength measures the maximum load the film can withstand before breaking, while elongation measures the film's ability to stretch without breaking. By maintaining optimum levels of tensile strength and elongation, our aluminum foil can withstand rigorous handling in a variety of applications, providing durability and reliability to our customers.
The surface quality of aluminum foil plays an important role in its usability and performance. Smooth, even surfaces facilitate spreading, reduce friction, and ensure even heat transfer during cooking and baking. It may also be required for some applications. Aluminum foil has a nonstick coating that adds convenience and prevents food from sticking. We place great emphasis on surface quality and offer a variety of options, such as non-stick plates, to enhance your cooking experience.
As a top manufacturer of aluminum foil, we will continue to provide quality products that meet the diverse needs of our customers. We understand the importance of metrics and quality control in providing quality products to our customers. Maintaining precise thickness and thickness control ensures optimal tensile strength and elongation, prioritizes surface quality and ensures even alloy composition to ensure high quality steel foil production that meets customers' diverse needs. Occasionally defects do occur, but our rigorous manufacturing processes and inspection protocols allow us to minimize them, adding value through our commitment to quality and customer satisfaction, ensuring reliable aluminum foil for a wide range of applications.