8079 aluminum foil is harder, stronger, and more resistant to corrosion and erosion than 1235 aluminum foil. 8079 aluminum foil is suitable for smaller applications, resulting in excellent properties. However, the corrosion resistance of 8079 allows it to easily withstand extreme conditions in extreme temperatures. Both have their advantages and can be most appropriately selected based on the manufacturer's production application.
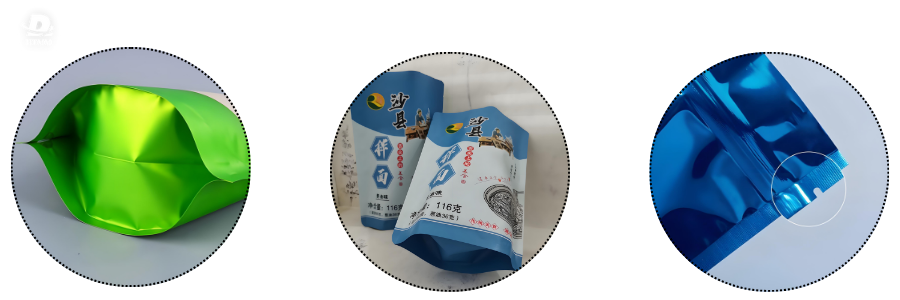
For larger items, such as various packaging bags, alloy 8079 is the best choice. The consistency prevents sticking and ensures a safe coating. Alloy 1235 is rougher and is more suitable for thicker foil shapes and smaller radii. The two blends can be used for different purposes.
The key is to understand the packaging complexity and the packaging and shipping requirements to determine whether maximum capacity and volume are important factors. Professionals like HTMM can help you evaluate your needs and recommend the best blend options.
As an aluminum foil manufacturer, HTMM has extensive experience producing both 1235 aluminum foil and 8079 aluminum foil. Our lab can test materials to ensure HTMM aluminum foil meets your requirements. Contact us to learn more about our services and how we can help you create a custom solution for your business.
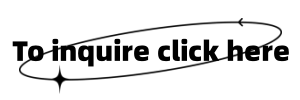
Both alloys can be used successfully in flexible applications. The key is to understand the specific needs and requirements of the project to determine whether maximum squareness (1235) or maximum strength (8079) is more important. Working with an experienced aluminum supplier can help you determine the best alloy choice.