Sources and refining of aluminum
The first step in our aluminum foil manufacturing process is to obtain high purity aluminum. Aluminum occurs naturally in the form of bauxite, which must be extracted and refined before it can be used. Raw Materials For Aluminium Foil Food Containers. We have long-term partnerships with the world's best bauxite mining companies that use sustainable and responsible practices. Our preferred bauxite source contains a high percentage of aluminum to increase the efficiency of the refining process.
.png)
After bauxite is mined, it undergoes a wet chemical refining process known as the Bayer process to extract aluminum hydroxide. Aluminum hydroxide is then calcined at high temperatures to form alumina. Aluminum oxide is electrolyzed in a large carbon-lined boiler, where it is separated from oxygen in its complex form. This electrolysis process can produce aluminum with a purity of up to 99%.
We work closely with aluminum refineries to ensure our aluminum foil sources meet the highest purity specifications. Container foil. Only aluminum with a purity of 99.85% or higher is accepted for the production of aluminum foil. Various tests are performed to check metal contamination such as iron, silicon, copper, zinc and nickel. Any impurities may affect the integrity, durability or formability of the final chip.
Rolling and processing operations
After casting and initial processing by our suppliers, the purified aluminum is sent to our manufacturing facility for rolling and processing. The aluminum is first heated to about 500 degrees Celsius and then rolled into thick coils using a large inversion mill. This process strengthens the processed aluminum, and reduces its thickness.
Successive rolling iterations further thin the aluminum profile to the desired foil thickness, which is typically between 0.006mm and 0.2mm. 3003 H24 Lubricant should be applied before rolling to promote uniform thickness reduction and a smooth surface. We only use food grade lubricants approved for indirect or direct food contact, such as esters.
Rolled aluminum coil is chemically treated and annealed to create the ideal material properties for flexible foil. The pickling process removes any surface oxide layer and prepares the surface for final operations. 8011 H24 Annealing treatment can relieve the internal stress generated during cold rolling. Some chips receive a hydrophobic coating treatment for additional non-stick properties.
Strict quality control tests are carried out after each production step to ensure compliance with our high standards and compliance with global food safety regulations. Modern testing equipment analyzes various parameters such as thickness consistency, surface quality, purity and mechanical properties. Only aluminum that meets our specifications is fired for slitting, slitting and rewinding into jumbo rolls.
Meet global demand with large rolls
As one of the largest aluminum foil suppliers in the market, we manufacture large rolls that meet a wide range of requirements from major food brands and industrial customers around the world. Our large rolls range from small rolls weighing 50 kg to large rolls weighing 1500 kg. The larger roll size reduces chip waste on high-speed production lines, and lowers shipping costs per ton compared to smaller rolls.
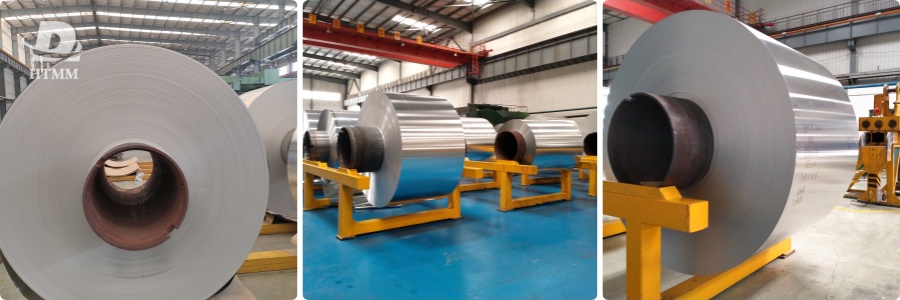
We currently have 4 production lines for rolling aluminum foil with widths ranging from 150 mm to 1500 mm. After forging and testing, the wide aluminum is cut and cut using highly automated equipment. The modern aluminum foil rewinding machine wraps aluminum foil into large, well-curved rolls at speeds exceeding 400 m/min. Core insertion technology supports our superior master cylinders with diameters over 1000mm.
Advanced packaging lines ensure that our aluminum foil is protected from damage or distortion during storage and shipping. Each surface roll is wrapped in plastic, wrapped in steel and protected in a wooden box. The large roll boxes are exported every month to Europe, America, Asia and the Middle East, serving large food production centers. We can count on just-in-time delivery from our manufacturing sites to ports around the world.
As this article explains, using only the highest quality raw materials and implementing strict quality control at every stage allow us to produce first-of-its-kind jumbo aluminum foil rolls that are trusted by leading brands. Our in-depth experience in aluminum sourcing and refining helps ensure the highest levels of purity. Combined with advanced rolling and processing processes, we develop aluminum foil with best-in-class barrier and flexibility properties. Customers around the world continue to rely on our rolls to produce and package snacks, frozen meals and a variety of other high-speed food applications.